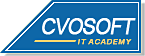
✒️SAP PP Programación y costeo de las órdenes de producción
SAP PP Programación y costeo de las órdenes de producción

Programación de una orden de producción
Los métodos de programación para planificación de la producción son los siguientes:
- La programación de ordenes previsionales generadas por le MRP con cálculo de fechas.
- Programación con tiempos de espera o leadtime para el calculo de las fechas de producción en base a fechas base.
La programación de los tiempos de espera puede ser usada para los siguientes propósitos:
- Programación de órdenes.
- Programación de hoja de ruta.
- Programación en el PS y PM.
*podemos activar los tiempos de espera en la programación del MRP, de manera que podamos determinar las necesidades de capacidad para las ordenes previsionales.
Elementos y tiempos de programación de las ordenes de producción
En la imagen 2.1 se muestran todos los posibles elementos que determinan el total de los tiempos de espera de una orden de producción.
Los tiempos de holgura sirven para varios propósitos, que son los siguientes:
- Tiempos de holgura antes de la producción: posponen las fechas usadas para la planificación de capacidades.
- Tiempos de holgura después de la producción: absorben retrasos.
La holgura de la orden puede ser predefinida, usando la clave de horizonte. La clave de horizonte se carga en el dato maestro de material y se mantiene en el customizing de las ordenes de producción debajo la configuración existente:
Customizing:
Ruta:
SPRO -> Producción -> Control de planta -> Operaciones -> Programación -> Definir clave de horizonte.
Aquí podemos ver las diferentes claves de horizonte, con sus tiempos de holgura, configuradas para cada centro.
Luego la clave de horizonte se carga en el maestro de material, en la vista de planificación de necesidades 2.
La duración de una operación compromete los siguientes elementos de tiempos:
- Tiempo en cola.
- Tiempo de configuración setup.
- Tiempos de procesamiento.
- Tiempos de desmontaje.
- Tiempos específicos de espera de procesos.
La duración entre movimientos de dos operaciones se asigna en la operación procedente de la hoja de ruta.
*si una orden de producción ejecuta o se genera desde un pedido de venta, debemos añadir los tiempos referidos al módulo de ventas SD:
Tiempos de una operación – Calculo de configuración, Procesamiento y Desmontaje
Para calcular la duración de preparación, tratamiento o desmontaje, debemos definir una categoría de capacidad para ser usada en la programación básica y una formula en el puesto de trabajo. Las duraciones son determinadas en base los valores prefijados y las formulas que se encargan de los mismos. Cuando se deben determinar las fechas operativas, el sistema toma en cuenta la disponibilidad de la capacidad teniendo en cuenta los tiempos de descanso y de programación.
Transacción: TRX: CR03 podemos visualizar el dato maestro del puesto de trabajo. (ingresando puesto de trabajo y centro -> En la solapa programación vemos el campo Clase de capacidad y debajo las duraciones.
Cada formula se puede configurar en el customizing:
RUTA:
SPRO -> Producción -> Control de planta -> Operaciones -> Programación -> Fijar definición de formula.
Los parámetros de la formula se configuran en el customizing:
RUTA:
SPRO -> Producción -> Control de planta -> Operaciones -> Programacion -> Definir parámetros de formula.
De estos parámetros hay dos timpos:
- Los que contienen un valor proveniente de un campo de operación .
- Los que contienen un valor prefijado que se carga en la notificación o como valor estándar de la operación de la hoja de ruta.
*IMPORTANTE: al momento de estipular la formula es importante tener en cuenta en el algoritmo que se prefije la división por la cantidad base.
Necesidades de capacidad de una operación
De la misma manera que se realizo anteriormente con la programación, para la capacidad, en base a los valores prefijados y otros parámetros el sistema usa las formulas para calcular las necesidades de capacidad (a través de las categorías de capacidad) de una operación.
Customizing de la programación
Ruta:
SPRO -> Producción -> Control de planta -> Operaciones -> Programación -> Especificar parámetros de programación.
Dentro de cada punto debemos definir los parámetros necesarios para la programación de las ordenes de producción para cada centro, clase de orden y responsable de control de la producción. Luego de cada registro hacemos doble clic y entramos a los detalles de la parametrización.
Costeo de las ordenes de producción
Cuando utilizamos el costeo en base a las órdenes de producción que se denomina Controlling de Objetos de coste o CO-PC-OBJ, un objeto de coste se gestiona para cada proceso de fabricación.
Los costos incurridos de una orden pueden ser calculadas manualmente o automáticamente. Para esto, debemos configurar los parámetros relacionados a la clase de orden en el correspondiente customizing. El objeto de costes de CO permite diferentes elementos de coste para las ordenes de producción.
Cálculo de planificación de costes
La planificación de los costes se define de acuerdo a lo siguiente:
- Elementos del coste: provee un resumen/ detalle de los elementos de costes individuales.
- Análisis: provee una visión general de las clases de costes, por ejemplo, los costes de material, costes de producción, gastos generales, etc.
- Estratificacion de costes: provee una visión general de los elementos de coste, sobre todo si se generan en base a la actividad (Costeo ABC).
 
 
 
Sobre el autor
Publicación académica de Victor Arias, en su ámbito de estudios para la Carrera Consultor en SAP PP.
Victor Arias
Profesión: Consultor Sap - Argentina - Legajo: QT61P
✒️Autor de: 26 Publicaciones Académicas
🎓Cursando Actualmente: Consultor en SAP PP
Certificación Académica de Victor Arias