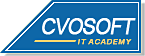
✒️SAP PP Programación y costeo de las órdenes de producción
SAP PP Programación y costeo de las órdenes de producción

PROGRAMACIÓN Y COSTEO DE LAS ÓRDENES DE PRODUCCIÓN
Programación de una orden de fabricación:
Los métodos de programación para planificación de la producción son los siguientes:
- Programación de Órdenes previsionales generadas por el MRP con cálculo de fechas.
- Programación con tiempos de espera o lead time para cálculos de las fechas de producción en base a las fechas base
Material Requirements Planning
- Separar la programación para órdenes previsionales
- Para el día
- Fechas extremas calculadas: Fecha inicio extremo, fecha fin extremo, fecha de inicio programación
- Programación: tiempos de fabricación propia (maestro de material)
- Alta performance
- Cálculo de necesidades de capacidad (a demanda)
Tiempos de Espera en la programación
- Utilización: para órdenes y hoja de ruta
- Al segundo
- Inicio en las fechas extremas: Planificación de necesidades, Manual.
- Determinación de las fechas de producción (fechas programadas): fecha de inicio, fecha de fin, fecha de liberación
- En base a: operaciones de la hoja de ruta
- Determinación de las necesidades de capacidad
Podemos usar estos métodos de programación para diferentes propósitos con diferentes resultados, solamente se calculan los tiempos de espera relacionados a fechas de operaciones y necesidades de capacidad.
La programación de los tiempos de espera pueden ser usados para los siguientes propósitos:
- Programación de órdenes
- Programación de la hoja de ruta.
- Programación en el PS y PM.
Además podemos activar los tiempos de espera en la programación del MRP, de manera que podamos determinar las necesidades de capacidad para las órdenes previsionales.
Elementos y tiempos de Programación de lasa órdenes de producción
Elementos que determinan el total de los tiempos de espera de una orden de producción:
Fechas de la orden:
- PS: fecha de inicio de la orden previsional
- SS: fecha de inicio de la producción
- SF: fecha de fin de la producción
- PF: fecha de fin de la orden previsional
- AD: fecha anticipada de disponibilidad
- LT: fecha de carga
- GI: fecha de la salida de mercancías
- DDD: fecha deseada de entrega
Fechas de la operación:
- ES: comienzo temprano
- SS: fecha de inicio tardío
- FE: fecha de fin temprano
- SF: fin tardío
Conceptos de los tiempos
- Lean time (tiempo muerto) de una orden por operación
- Tiempo flotante por orden / operación
- Lean time por operación
- Tiempo interoperacional
- Tiempo de procesamiento en ventas y distribución.
Los tiempos de holgura sirven para varios propósitos, que son los siguientes:
- Tiempos de holgura antes de la producción: posponen las fechas usadas para la planificación de capacidades.
- Tiempos de holgura después de la producción: absorben los retrasos.
La holgura de la orden puede ser predefinida, usando la clave de horizonte. La clave de horizonte se carga en el dato maestro del material y se mantiene en el customizing de las órdenes de producción.
Clave de horizonte: determina los tiempos de aprovisionamiento al momento de definir las fechas para las cuales se crearán las órdenes previsionales esta clave define el tiempo de anticipo, el tiempo de seguridad y el horizonte de liberación. Esta clave se configura a nivel centro y se asigna al maestro de material en la vista de planificación de necesidades.
SPRO/Producción/Control de Planta/Operaciones/Programación/Definir clave de horizonte
La duración de una operación compromete los siguientes elementos de tiempos:
- Tiempo en cola
- Tiempo de configuración setup
- Tiempo de procesamiento
- Tiempo de desmontaje
- Tiempos específicos de espera en procesos.
La duración entre movimientos de las operaciones se asigna en la operación precedente de la hoja de ruta.
Si una orden de producción de ejecuta o se genera desde un pedido de venta, debemos añadir los tiempos referidos al módulo de ventas SD.
Tiempos de una operación - Cálculo de Configuración, Procesamiento y Desmontaje.
Para cálcular la duración de preparación, tratamiento o desmontaje, debemos definir una categoria de capacidad para ser usada en la programación básica y una fórmula en el puesto de trabajo. Las duraciones son determinadas en base a los valores prefijados y las fórmulas que se cargan a los mismos. Cuando se deben determinar las fechas operativas, el sistema toma en cuenta la disponibilidad de la capacidad teniendo en cuenta los tiempos de descanso en la programación.
Con la transacción CR03 podemos ver el dato maestro del puesto de trabajo, al ingresar cargamos el puesto de trabajo y el centro, el la solapa programación, podemos ver la clase de capacidad y las fórmulas para cada tiempo. Cada frórmula se puede configurar en la siguiente dirección del customizing.
SPRO/Producción/Control de Planta/Operaciones/Programación/Fijar definición de fórmula
Dentro de ese punto podemos ver que la fórmula es una operación aritmética que contiene variables, estas variables son parámetros.
Los parámetros para las fórmulas se configuran en este punto de customizing:
SPRO/Producción/Control de Planta/Operaciones/Programación/Definir parámetros de fórmula
Hay dos tipos de parámetros:
- Los que contienen un valor proveniente de un campo de la operación (ejemplo cantidad de la operación)
- Los que contienen un valor proveniente de valor prefijado que se carga en la notificación o como valor estándar de la operación de la hoja de ruta.
Los provenientes de un valor prefijado, deben estar contenidos dentro de la clave de valor prefijado, que se carga en el puesto de trabajo y se heredará en la hoja de ruta que use este puesto.
Necesidades de capacidad de una operación
De la misma manera que se realizó anteriormente con a programación, para la capacidad, en base a los valores prefijados y otros parámetros, el sistema usa las fórmulas para calcular las necesidades de capacidad (a través de las categorías de capacidad) de una operación.
En el customizing:
SPRO/Producción/Control de Planta/Operaciones/Programación/Especificar parámetros de progrmación
Dentro de este punto debemos definir los parámetros necesarios para la programación de las órdenes de producción para cada centro, clase de orden, Responsable del control de la producción. Dentro del detalle podemos configurar los parámetros para la combinación antes descrita.
Costeo de las órdenes de producción
Cuando utilizamos el coste en base a órdenes, que se denomina controlling de objetos de coste o CO-PC-OBJ, un objeto de coste se gestiona para cada proceso de fabricación.
Cabecera de la orden
Operaciones
- Costes de Producción (fabricación propia, procesamiento externo)
Componentes
- Costes de Material ( material de stock, Material no de stock)
Costes
- Gastos Generales
- Costes de proceso
Los costes incurridos de una orden pueden ser calculados manualmente o automáticamente. Para esto, debemos configurar los parámetros relacionados a la clase de orden en el correspondiente customizing. El objeto de coste de CO permite diferentes elemento de coste para las órdenes de producción.
 
 
 
Sobre el autor
Publicación académica de Roberto Ramon Bouchet, en su ámbito de estudios para la Carrera Consultor en SAP PP.
Roberto Ramon Bouchet
Profesión: Administrativo de Producción - Argentina - Legajo: NG47Q
✒️Autor de: 30 Publicaciones Académicas
🎓Egresado del módulo:
Disponibilidad Laboral: FullTime
Presentación:
Buenas mi nombre es roberto bouchet soy licenciado en administración de empresas y estoy ansioso por iniciar es un sistema con mucho potencial
Certificación Académica de Roberto Bouchet